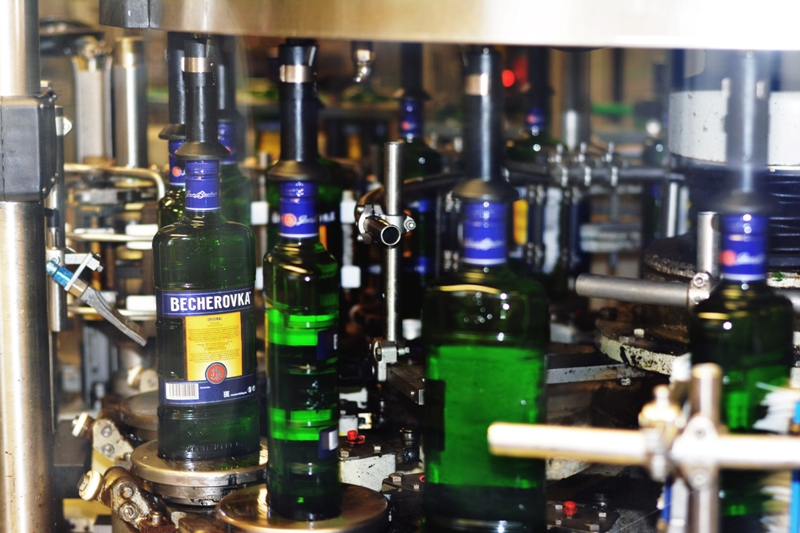
Zavedení reportingu a automatického sběru dat z plnicí linky v Becherovce znamenalo snížení prostojů
Známý výrobce tradičního likéru Jan Becher - Karlovarská Becherovka, a.s. chtěl odstranit zbytečnou práci obsluhy při manuálním zadávání výrobních dat a jejich následném vyhodnocování. Firma zvolila jako dodavatele společnost KROPF Solutions.
Známý výrobce tradičního likéru Jan Becher - Karlovarská Becherovka, a.s. chtěl odstranit zbytečnou práci obsluhy při manuálním zadávání výrobních dat a jejich následném vyhodnocování. Firma zvolila jako dodavatele společnost KROPF Solutions, která dodala systém založený na softwaru zenon, jenž umožní komunikovat s téměř kteroukoliv řídicí jednotkou nebo ERP systémem, protože disponuje více než 300 různými přímými ovladači. Díky tomu je Karlovarská Becherovka do budoucna nezávislá na použitém hardwaru a samozřejmě také strojích.
Důvody rozhodnutí
Než si výrobce slavné Becherovky zenon pořídil, tak bylo nutné mít u každého stroje papír s tužkou. Když pak například u plniče praskla láhev, operátor ji musel vyjmout, vyčistit stroj a znovu jej spustit. Jelikož obsluha linky obvykle neměla spuštěny stopky, tak čas odstávky mnohdy jen odhadovala. Z původně zapsaných 5 minut mohlo být nakonec minut třeba 10. Tady už mohla vzniknout první chyba a směnový mistr opět do tabulky uvedl, že směna trvala určitou dobu, z toho čistá výroba opět nějaký čas. Z papíru vyčetl poznámky operátorů, zaznamenal je do excelové tabulky, ale ani zde se nedala vyloučit chyba člověka. Excel samozřejmě tyto údaje spočítal, ale to však neposkytovalo uživatelský komfort a s daty se pak nedalo ani jednoduše pracovat.
„Pokud bychom chtěli takto získaná data statisticky analyzovat, znamenalo by to pro nás mnoho další práce a především výsledek by nakonec s velkou pravděpodobností neodpovídal skutečnosti. Díky tomuto systému máme úplný přehled o nejčastějších problémech a poruchách, jejich opakovaném výskytu (nebo jejich opakování) a délce jejich trvání. Navíc máme všechny potřebné informace k dispozici během několik málo vteřin. Můžeme tak okamžitě reagovat na neočekávané události a zamezit tak zbytečným prostojům ve výrobě. Navíc nyní již zaměstnanci nemusí myslet na to, jak dlouho zastavení trvalo a můžou se věnovat tomu hlavnímu, což je odstranění problému a co nejrychlejší opětovné zahájení výroby. Přesně víme, kde jsou naše slabá místa. Nějaký problém se může opakovat tak často, že by se mohlo zdát, že se jedná o největší důvod zastavení, ale analýzou dat v přednastaveném reportu lehce můžeme zjistit, že frekvence výskytu je opravdu velká, ale vlastní časová ztráta je oproti jiným zanedbatelná, jelikož jednotlivé zastavení trvá několik málo sekund. Hlavním problémem pak může být věc, které se opakuje jednou za den, ale výroba je kvůli němu zastavena na desítky minut, “ řekl Tomáš Bryzgal, ředitel výrobního závodu Jan Becher - Karlovarská Becherovka, a.s.
Firmě tedy nešlo pouze o to, získat záznamy samotné, jelikož podobnými informacemi disponovala již dříve, i když zadávání dat probíhalo z větší části manuálně. Cílem bylo mít data, se kterými je možno pracovat za účelem vyšší efektivity výroby. Díky přesným datům je pak možné stanovit efektivitu výroby a cíl. „Dostat se k vytýčeným cílům můžeme tak, že vyřešíme problémy, které nám program identifikoval. Program je tedy pomocník, který pomáhá stanovit objem výroby pro dané období a to vede i k plánu investic do údržby, protože víte, se kterým strojem jsou nejčastější problémy a můžete se věnovat i prediktivní údržbě. Vždy je to ale samozřejmě také o lidech, protože pokud by vám program dodával špičkové reporty a nikdo by s nimi nepracoval, byly by k ničemu. Program máme nasazen v plném provozu od ledna 2016, ale detailně se získanými daty zabýváme na denní bázi až posledních 10 měsíců a je to vidět i na našich výsledcích,“ popisuje Tomáš Bryzgal.
Jak systém pracuje
Komunikace mezi jednotlivými segmenty linky je realizována pomocí Ethernetu. Zařízení disponující pouze sériovým rozhraním byla vybavena převodníky MPI/Ethernet. Značnou časovou úsporu přinesla funkce pro přímý import proměnných (z jednotlivých PLC programů). Vlastní server je v tuto chvíli určen především ke sběru dat, která dále prezentuje pomocí klientů. Jedním z nich je přehledný dotykový panel s FULL HD rozlišením, který je nainstalován přímo u plniče a nabízí stejná data (1:1) jako již zmiňovaný server. Další přístup k datům a funkcím poskytuje WEB server, který nabízí informace také manažerům, jak v rámci závodu, tak mimo něj. Záleží pouze na uživatelích, zda budou dále data prezentovat pomocí webového prohlížeče, mobilní aplikace či dashboardu, protože nejsou omezeni výběrem operačního systému, ani rozlišením.
Přihlášení uživatelů je zajištěno pomocí čipů. Na serveru je k dispozici také přímý komunikační ovladač pro čtečku těchto čipů, a tudíž není zapotřebí žádné další řídicí jednotky. V systému mají administrátoři možnost nastavení různých uživatelských oprávnění. Uživatelé získávají kompletní přehled o funkčnosti jednotlivých oblastí výroby doplněný o reporty (dle vlastního výběru) a možnosti manuálního zadávání dalších informací týkajících se výroby. Zaměstnanci společnosti tak mají k dispozici jedinečný nástroj, který je informuje o celém průběhu výroby, pomáhá jim dále analyzovat data a vyhledávat slabá místa produkce. Mohou tak okamžitě reagovat na vzniklé události a díky automatickým výkonnostním ukazatelům ušetří nemalé prostředky. Jako další krok Karlovarská Becherovka zvažuje možnost integrovat data o spotřebách energií a existujícího systému využít zároveň jako EMS.
Jak projekt pomáhá při výrobě nejen Becherovky
Systém je využíván ke sběru dat a jakákoliv porucha či zastavení linky se automaticky zaznamenává. V Becherovce mají nastaveno, že pokud je zastavení delší než 10 sekund, tak systém sám vyhodnotí, kde se stala chyba. Pokud se jedná o důvod zastavení, či poruchu, kterou je možné identifikovat automaticky přímo z řídicího systému (například zaseklá láhev, případně nedostatek materiálu), je tato informace poskytnuta obsluze, která tuto zprávu vyhodnotí. Nastávají ale také situace, kdy systém důvod nerozpozná, protože zastavení bylo způsobené přímo operátorem. V tomto případě má operátor k dispozici předdefinované „důvody zastavení“, které je možno zadat do systému manuálně.
„Máme tak detailní přehled o všech důvodech zastavení, která se odehrají během dne, týdne, měsíce či roku.Takto získané informace jsou poté výborným základem pro reporty za libovolné období pro jednotlivé výrobky. Víme také, kolik času jsme ztratili neplánovanými odstávkami a jak dlouho trvala plánovaná zastavení, například z důvodu přenastavení linky pro různá balení a jednotlivé trhy. Známe také efektivitu OEE, kterou máme nastavenu podle definice nastavené v koncernu Pernod Ricard, abychom byli porovnatelní s ostatními závody firmy. Každý den dostáváme report za uplynulý den, kdy OEE bylo například 63 % a kvalita výroby 99,5 %. Poté si systém sám dopočítává informace, které získává z řídicího systému, kdy do linky bylo vloženo například 50 000 láhví, ale do kartonovačky jen 49 800. Dopočítá rozdíl 200 láhví, které musely být vyřazeny například z důvodu poškození láhve či etikety,“ vysvětluje Tomáš Bryzgal.
Díky novému systému je nyní možné si kdykoliv stáhnout reporty ve formě grafů či tabulek. „To byl pak jeden z hlavních benefitů tohoto systému, kdy jsme získali přesně to, co jsme chtěli. V průběhu tvorby projektu nám realizátor nikdy neřekl, že něco nejde, protože takto to máme přednastavené. Když jsme totiž hledali jiné dodavatele, kteří by nám mohli dodat software na efektivní řízení záznamů o výkonnosti linky, tak mnoho systémů už bylo předpřipravených a nebyla zde tak velká možnost úpravy systému přesně dle našich požadavků, což vzhledem ke specifikům naší výroby nebylo akceptovatelné,“ podotkl Tomáš Bryzgal.
Významným benefitem je také omezení prostojů. Jak bylo uvedeno výše, dřívější manuální zaznamenávání odstávek linky zdržovalo nejen operátory, ale i směnového mistra, který musel s daty pracovat po skončení činnosti linky. Zavedení tohoto systému založeném na zenonu tyto činnosti odstranilo.
Objektivnější porovnání výkonnosti v rámci koncernu
Výsledkem těchto snah je, že se výrobní závod v Karlových Varech v parametrech OEE dle standardů Pernod Ricard dostal z 55,5 % na hodnotu 61,5 %. Nyní se Karlovarská Becherovka v rámci koncernu Pernod Ricard dostala do lepšího průměru mezi všemi ostatními závody, pokud se týká celkové efektivity provozu plnicí linky. „Toto považuji za opravdový úspěch, protože na rozdíl od naprosté většiny ostatních továren Pernod Ricard máme jen jednu plnicí linku, což přináší mnoho komplikací, jelikož při každé změně výrobku musíme přestavovat linku. Větší výrobci mohou mít vyšší efektivitu způsobenou právě vyšším počtem výrobních linek. I náš obalový materiál ve formě oválné láhve s několika embossy a specifická etiketa s prodlouženými pásky nepatří k nejjednodušším na zpracování,“ popisuje Tomáš Bryzgal.
Mozek výroby Becherovky by mohl být opět zenon
Karlovarská Becherovka může do budoucna i uvažovat o dalším rozšíření systému zenon o funkci řízení chodu plnicí linky. Systém je schopen dát požadavek na snížení nebo zvýšení rychlosti plniče nebo jakéhokoliv dalšího stroje a v ideálním případě odhalí, ve které části linky je případný technický problém. Pokud je třeba závada na kartonovačce, systém zpomalí plnič z 10 000 ks lahví za hodinu na 3 000 ks lahví a po odstranění závady zase najede na plný výkon. Ideální rychlosti výroby na jednotlivých strojích jsou přednastaveny a reagují na danou situaci. Rychlost výroby tak není určována operátory, jako je to nyní běžné. „Musíme si ale nejprve vyhodnotit, zda by to pro nás mělo žádoucí efekt v porovnání s investicí,“ dodává Tomáš Bryzgal.
Autor: Petr Pohorský, Automatizace v potravinářství