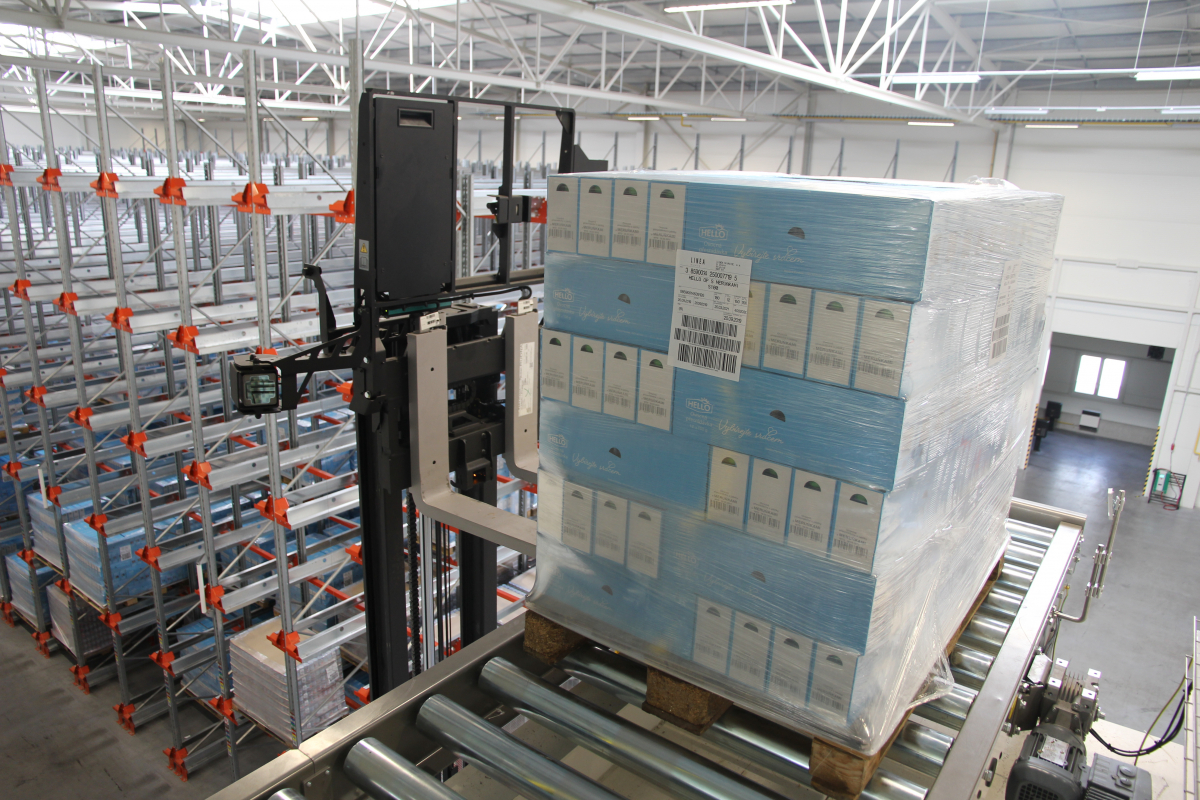
Linea Nivnice automatizuje interní logistiku
Projekt souvislé automatizace toku zboží od čtyř linek na výrobu dětské výživy až před korbu nákladního vozidla byl ve společnosti Linea Nivnice, a. s. na moravsko-slovenském pomezí rozdělen na tři etapy.
Projekt souvislé automatizace toku zboží od čtyř linek na výrobu dětské výživy až před korbu nákladního vozidla byl ve společnosti Linea Nivnice, a. s. na moravsko-slovenském pomezí rozdělen na tři etapy. Už druhá etapa byla dokončena začátkem září 2019, když byl do plného provozu uveden první retrak Autopilot RAE200, důležitý díl propojující výrobu a centrální sklad. Cílem celého řešení je zrychlení manipulace, vyšší bezpečnost při manipulaci ve výrobě i ve skladu a celkové snížení provozních a personálních nákladů.
Ze třetí etapy je zatím zprovozněna jen její poloautomatická část v podobě systému Radioshuttle. Její dokončení, tedy přímé navazující automatické zaskladňování prostřednictvím retraku RAE200 a souhra automatu s manipulační jednotkou Radioshuttle, je naplánováno do konce listopadu letošního roku.
Zaskladňování zatím vykonává standardní retrak BT Reflex s obsluhou. Petr Malík, technický ředitel společnosti Linea Nivnice, stál u zrodu myšlenky automatický provoz vybudovat. Popisuje vývoj záměru: „Z původního plánu zautomatizovat odvoz od výrobních linek a pomocí dvou výtahů a dopravníkového krčku palety dopravit do skladu, kde budou konvenčně zaskladněny do vjezdových regálů, se projekt po konzultacích s Toyotou a představení všech možností automatizace a systému Radioshuttle posunul do současné podoby. Konkurence odmítla automatické řešení pro nepřipravenost nabídnout.”
Radioshuttle přesvědčil, automatizace rozhodla
Petr Malík uvádí, že jako nejlepší typ skladu nakonec vyšel systém bezuličkového skladování Radioshuttle s režimem FIFO, takže se Linea rozhodla pro Toyotu jako komplexního dodavatele - vozíků i regálového systému: „Sortiment dětské výživy představuje relativně malý počet položek (3 druhy obalů – kapsičky 100 ml a 200 ml, sklo/různé příchutě), ale s většími šaržemi. Jde o naplnění jednoho ze základních předpokladů pro instalaci vysokohustotního bezuličkového regálového systému, v kterém nejsou jednotlivé palety přístupné, a proto je důležité skladovat v jednom regálovém tunelu jen jeden druh zboží. Odbourání uliček, vysoké využití objemu skladu (až 85 %) a rychlost manipulace (obslužný vozík - automat nebo konvenční vozík – odváží paletu, manipulační jednotka Radioshuttle mezitím manipuluje v tunelu další paletu) činí z tohoto systému vysoce produktivní záležitost s rychlou návratností investice.“
Regálový systém se dvěma obslužnými uličkami se skládá z 28 řad s 6 výškovými úrovněmi. Hloubka regálových tunelů je 21 palet. Celkem lze v regálovém systému uskladnit 3 500 palet. Aktuálně jsou k dispozici 3 jednotky Radioshuttle. Jednotky budou podle potřeby využívány jak pro zaskladňování, tak pro vyskladňování. Přenášení jednotek mezi tunely bude tedy velmi časté.
„Jsme rádi, že jsme postupně dospěli k řešení s automatickou obsluhou systému Radioshuttle, protože přemisťování jednotky mezi tunely pomocí běžného vozíku jsme považovali za rizikové. Jde o drahé zařízení, které může neopatrný řidič poškodit. Autopilot je přesný, nepoškodí čidla jednotky, nenapíchne ji vidlicemi, nespadne mu z vidlic, nesrazí se s regálem. Manipuluje plynule, bez prudké akcelerace při rozjedu vozíku, při brzdění, při zdvihu nebo spouštění stožáru. Bude fungovat bez chyb a bez ohledu na denní dobu. První stejně jako tisící jízdu,“ dodává Petr Malík.
Etapy a procesy
1. etapa - v provozu od června 2019
Odebrání palety z dopravníku za paletizačním automatem a jeho převoz na dopravník vedoucí k ovinovacímu stroji a k výtahu, který paletu v dalších fázích vyveze na dopravník spojující výrobní provoz a sklad - manipulaci, vykonává zakladač Autopilot SAE160.
2. etapa - v provozu od září 2019
Ze spojovacího dopravníku ve výšce 7 metrů paletu odebere automatický retrak Autopilot RAE200 a buď ji zaskladní (3. etapa – viz dále), nebo v případě okamžité expedice ji umístí na předem určené místo v expediční zóně. Momentálně automat paletu určenou k zaskladnění odloží na určené místo (Deep
Stack Line), odkud ji převezme a zaskladnění provede manuálně řízený vozík.
3. etapa - fáze zaskladnění
První retrak paletu po odebrání z dopravníku odveze a zaskladní ji v regálovém systému Radioshuttle do vybraného kanálu – přitom bude on-line komunikovat s manipulační jednotkou Radioshuttle a ověřovat si její polohu - v případě potřeby si automat bude nejprve přemisťovat manipulační jednotku mezi jednotlivými tunely regálového systému- jednotka poté automaticky zaskladní paletu na první volné místo v regálovém tunelu.
3. etapa - fáze vyskladnění
Druhý retrak Autopilot RAE200 na základě objednávek z WMS systému paletu vyskladní a odveze na předem určené místo v expediční zóně (Deep Stack Line). V rámci 3. etapy probíhá programování komunikace Autopilot / Radioshuttle – systém Radioshuttle je v provozu od března 2019.
Jak se tvoří objednávka?
Oříškem bylo vyřešení kooperace, propojení toku informací a interakce více technologií od řady dodavatelů (WMS, Autopilot, Radioshuttle, paletizátor, ovinovací stroj, výtahy, dopravníky) a bezchybné svázání jejich činností do logického sledu. Jde o vyšší úroveň propojení než v jiných aplikacích a dá se říci, že se jedná o unikátní řešení, jedno z prvních v Evropě. Využili jsme infrastrukturu zákazníka (úspory za hardware), na druhou stranu řídicí software vozíků Autopilot vyžadoval určité přizpůsobení pro komunikaci s jednotkami Radioshuttle přes bezdrátovou síť. Klíčem pro dobré fungování celého řešení je moment vytvoření objednávky na odvoz a zaskladnění palety a předání této informace automatickým vozíkům, a to každému jen tu část, kterou potřebuje znát.
Objednávku vytvoří Warehouse Management Systém (WMS) zákazníka. Stacker dostane informaci, že je paleta z výroby připravena k odebrání, retrak dostane z WMS informaci, jaká paleta přijede na spojovací dopravník a kam ji má v regálovém systému uložit (a jestli vůbec, protože může být určena k přímé expedici - další úkon, který automat na rozdíl od člověka nikdy nesplete).
Petr Fiala, aplikační technik Toyoty, jehož úkolem bylo vytvoření a naprogramování logiky zpracování těchto informací a jejich přesné rozpracování do jednoho každého kroku/pohybu obou automatů (věcně i časově), vysvětluje: „Ve chvíli, kdy paleta vyjede z výroby do paletizátoru,je zabalena a opatřena štítkem, který je odeslán do WMS. Ten vyrobí objednávku pro odeslání do skladu a zaskladnění, a pošle ji do automatu SAE160, do ovinovacího automatu a k automatické etiketovačce. Impuls odvézt palety dostává vozík ve chvíli, kdy jsou na dopravníku za paletizátorem připraveny dvě palety stejného zboží. Z domácí stanice dojede k výstupnímu dopravníku a postupně odveze obě na dopravník směřující k ovinovačce a do výtahu. Na určené pozici odešle informaci o dokončení úlohy. A dopravník může chystat další paletu do pozice pro odebrání. Pokud nemá další úkol, odjede zpátky do domácí stanice, což je v tomto případě současně i nabíjecí místo. Každá zastávka je využita k nabíjení, protože lionky krátké a příležitostné nabíjení umožňují.“
„Výtah vyveze paletu do výšky 7 metrů a předá ji na další dopravník, který již ústí do skladu. Na konci dopravníku je kontrolní kamera, která načte a zkontroluje obsah štítku a potvrdí automatickému retraku, že paleta může být zaskladněna a kam. Před odebráním palety ze spojovacího dopravníku si musí retrak ověřit několik věcí. Zda je tunel, kam má zaskladnit volný, zde je v tunelu k dispozici manipulační jednotka, a pokud ne, musí ji tam nejdříve přemístit. Jiný postup proběhne, když automat zjistí, že je v tunelu místo jen pro jednu paletu. Zde musí automat jednotku Radioshuttle nejdříve vyndat, a poté teprve zaskladnit poslední paletu. Opačný postup by znamenal uvěznění podvozku v tunelu. Maximální kapacita celého řešení je 20 palet za hodinu, což odpovídá špičkovému provozu. Standardní výkon se pohybuje kolem 12-16 palet za hodinu.“
Automaty chtějí mít neustále jasno na 100 %. Provádí neustálé bezpečnostní kontroly a vysílají dotazy, ověřují svoji pozici vůči regálům nebo dopravníkům, načítají svou pozici před každým nabráním nebo uložením palety, ověřují si připravenost jiné části systému (mohu vjet do dopravníku?, je paleta připravena?). Dotazy směrem k externím systémům (WMS) probíhají přes Web Services. WMS odpoví například na základě informace z paletizátoru, z dopravníku nebo na základě záběru z kontrolní kamery nebo z informace ze senzoru monitorujícího pohyb palety na dopravníku. V běžném provozu mohou vznikat nenadálé situace, například poškození etikety, nečitelná etiketa, výpadek proudu, požární poplach, zablokovaná trasa, a vozík musí vědět, jak se má v každém jednotlivém případě zachovat. Reaguje vždy na splnění nějaké definované podmínky.
Nabíjení podle definovaných podmínek
Například do nabíječky odjede retrak automaticky v případě splnění podmínky o minimální přípustné úrovni nabití - ve společnosti Linea je to 30 %. Když se li-ionová baterie vybije pod 30 %, dokončí Autopilot poslední aktivní/probíhající objednávku, další zatím neakceptuje a odjede se dobít. Nabíječku opustí, jakmile dosáhne nějaké další minimální vrchní nastavené úrovně, například 60 %. Z toho vyplývá, že bude v nabíječce 15-20 minut (může být i déle, limitně až do 100 %, pokud neobdrží nový úkol). Mezitím se mu mohou kumulovat palety, nebo vyřízení převezme jiný vozík, pokud je jich víc. Po přestávce to hravě dožene. Lidé si zvykli, ekonomika řešení vychází velmi dobře. Automatizace procesu vylepšila efektivitu procesu, zjednodušila personální politiku na tomto úseku výroby a skladování a radikálně zvýšila bezpečnost celého procesu, což ocenili i lidé.
„Pracovníci v provozech ale měli zpočátku z automatů obavy. Podle zkušeností Toyoty si prošli obdobným vývojem jako v jiných firmách, kde byly automaty uvedeny do provozu. Prvotní strach (zvládnu to, když po mě bude vozík něco chtít?, nemohu ho poškodit?) vystřídala úleva (obvykle nic nechce nebo je to řešitelné) a fáze testování (co snese, co udělá, když....). Nakonec všichni vozík plně přijali jako součást pracovního prostředí. Zjistili, že obvykle stačí, když mu nebudou překážet.
K hladké implementaci po technické i lidské stránce přispělo i rozfázování na více etap a postupný náběh každé z nich,“ říká Petr Malík a na závěr shrnuje: „Ve třísměnném provozu ušetříme 3 až 3,5 pracovníka na směnu (řidiče vysokozdvižných vozíků, retrakáře, manipulanty u výrobních linek nebo výtahů). Navíc nemusíme řešit například nezájem lidí o víkendové směny. Zejména mladí lidé upřednostňují volno před výdělkem, a to navzdory nadstandardním příplatkům. Automaty se také nehádají, nemarodí, neprotahují si přestávky, nekouří, nepotřebují školení. Odpadne mnoho neproduktivních činností manažerů. Uvědomujeme si, že jsme společně s Toyotou vymysleli moderní a efektivní řešení a už se těšíme na dokončení poslední etapy.“
Autor článku a fotografií: Toyota Material Handling CZ s.r.o.
Kontakt:
Aleš Hušek
GSM: +420 728 360 370
ales.husek@cz.toyota-industries.eu