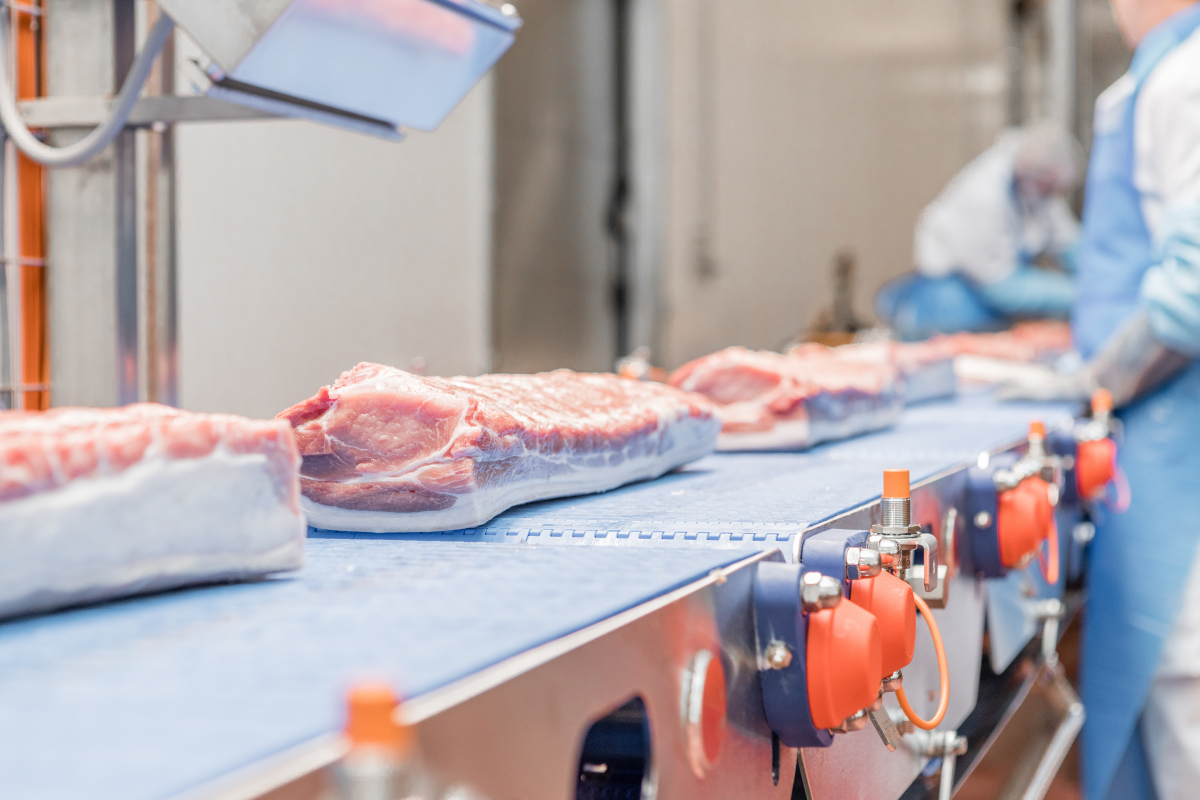
Automatizace ruku v ruce s tradicí u výrobce slaniny HANDL v Tyrolsku
Na 5000 tun slaniny opustí během jednoho roku nový moderní výrobní závod firmy HANDL TYROL GmbH v Haimingu v rakouském Tyrolsku.
Na 5000 tun slaniny opustí během jednoho roku nový moderní výrobní závod firmy HANDL TYROL GmbH v Haimingu v rakouském Tyrolsku. Řešení automatizace celého závodu, implementované společností ematric – stříbrným partnerem COPA DATA, založené na softwarové platformě zenon, umožňuje velice efektivní výrobu zdejších tradičních delikates.
Po tisíce let člověk dotvářel do dokonalosti umění konzervace masa pomocí nakládání do soli, sušení a uzení. Kombinace masa se solí, ohněm, vzduchem a kořením spoluvytváří specialitu zvanou Tyrolská slanina (Tiroler Speck). Ta je populární především v alpských oblastech jako energeticky vydatné občerstvení. Pravá Tyrolská slanina je tvořena kombinací severské metody uzení se středozemní metodou sušení s využitím malého objemu soli a studeného kouře, hodně čerstvého vzduchu a několikatýdenní dobou zrání. Jednoznačně rozeznatelná je tato specialita díky udělené ochranné známce Evropské Unie s označením g.g.A. -chráněné zeměpisné označení (CHZO).
Nejznámější a největší výrobce Tyrolské slaniny CHZO je firma HANDL TYROL. Rodinná firma založená v roce 1902 zaměstnává kolem 550 zaměstnanců ve čtyřech závodech. Ročně vyprodukuje kolem 15000 tun originální Tyrolské slaniny, šunky, salámů a dalších uzenin, které exportuje do 25 zemí světa. Vedle zaručené kvality a skvělé chuti svých produktů vděčí HANDL TYROL za svůj úspěch častým inovacím výrobních technologií a variaci svých produktů.
Tradice na nový způsob
Proces výroby Tyrolské slaniny CHZO pro prodej v maloobchodech zabere několik měsíců. Po nasolení se kusy masa nechávají tři týdny odležet v chladné místnosti, následně jsou uzeny studeným vzduchem z bukového dřeva s teplotou kolem 20 °C. Maso je dále sušeno vzduchem osm až šestnáct týdnů. V tomto okamžiku již ztratilo kolem 40 procent původního objemu. Po zformování a opracování je krájeno na typicky tenké plátky a baleno.
Pro oslovení nových trhů a uspokojení rostoucí poptávky se představitelé HANDL TYROL rozhodli vystavět nové výrobní zařízení pro své klíčové produkty šunku a slaninu z kotlety (Kareespeck), kde, dle své vlastní definice pro inovaci, budou vyrábět původním postupem, ale po novém způsobu. „Osvědčený, efektivní a částečně předepsaný výrobní proces bude zachován,“ vysvětluje cíle projektu Karl Christian Handl, výkonný jednatel společnosti HANDL TYROL GmbH. „Současně má vysoký stupeň automatizace založený na principech Průmyslu 4.0 umožnit flexibilní a energeticky efektivní výrobu velkého množství produktů a usnadnit dodržování vysokých standardů kvality a povinností protokolování výrobního procesu.“
Ověřeno v původních provozech
S cílem integrovat technologii budov do celkové automatizace vybavila společnostH ANDL již před vlastní výstavbou nové výrobní haly určené pro výrobu slaniny svá stávající výrobní místa moderním řídicím systémem. „Inventarizace ukázala širokou paletu různých řídicích a automatizačních systémů, které bylo zapotřebí integrovat,“ vzpomíná Rainer Haag, jednatel firmy ematric, partnera COPA DATA na úrovni stříbrné partnerství. „Díky své schopnosti komunikovat s prakticky jakýmkoliv představitelným systémem třetí strany padla volba na zenon.“
Na základě osvědčené softwarové platformy firmy COPA DATA byl vytvořen řídicí systém pro vytápění, vzduchotechniku, chlazení a další technické vybavení budov, které přímo souvisí s výrobou. Během několika let integrovali automatizační specialisté z firmy ematric postupně čím dál více stávajících systémů za pomoci platformy zenon. Vznikl tak komplexní systém pro řízení výroby a technického vybavení budov, který pracuje s daty napříč všemi závody.
Jednotné systémové prostředí
Jedním z cílů plánování nového výrobního závodu byla integrace výrobního zařízení a techniky budov do jednoho kompletního automatizovaného systému pro celý podnik. Představitelé firmy HANDL hledali jednotné systémové prostředí s cílem vybudování nadřazeného řídicího střediska, které umožní řídit veškeré výrobní procesy a zajistí jednoduchou a bezchybnou výměnu dat s podnikovým systémem úrovně ERP. Dalším očekáváním plynoucím z nasazení systému bylo snížení úsilí potřebného pro vytvoření obsáhlé dokumentace pro vyžadované protokolování průběhu výroby.
„Měli jsme již skvělou zkušenost s implementací softwarové platformy zenon integrátorem ematric,“ říká Karl Christian Handl. „Proto jsme se rozhodli pokračovat touto cestou i pro novou výrobní halu.“ Na rozdíl od předchozích projektů zde bylo zapotřebí od počátku zahrnout veškeré procesní vybavení, výrobní stroje a dopravníkové technologie, včetně automatizovaného bezobslužného dopravního systému.
Vedení firmy HANDL naplánovalo systém do největších detailů, aby zajistilo, že dojde k úspěšnému dosažení vytyčených cílů. Stroje, systémy a vedlejší jednotky byly navrženy až poté, kdy byl externí firmou pomocí počítačové simulace důkladně zmapován očekávaný tok zboží. Rozměry budovy a její rozvržení následovalo až poté. Digitální dvojče systému, založené na tomto počítačovém modelu, poskytlo vynikající základnu pro projektové práce techniků ematric.
Transformace automatizační pyramidy
Vedle dobré zkušenosti z provozu ve stávajících závodech a schopnosti přímého propojení mezi systémy ERP a SCADA sehrála významnou roli při výběru řešení také schopnost redundance systému zenon a jeho bezpečnost. Software může být provozován se záložním serverem a poskytuje značné množství možností pro ovládání přímo z klientského systému. „Navrhli jsme celý systém takovým způsobem, že i v případě totálního selhání serveru mohou jednotlivé stroje dále efektivně fungovat,“ vysvětluje HMI/SCADA specialista Daniel Weiskopf z firmy ematric. „To také usnadňuje provádět činnosti údržby a aktualizace bez přerušení výrobních procesů a ztráty dat.“
Pro zajištění bezztrátového sběru dat s vysokou spolehlivostí provozu převrátily firmy HANDL a ematric tradiční automatizační pyramidu vzhůru nohama. Po konzultaci s techniky z COPA DATA bylo vše mezi úrovní ERP a MES systémů a výrobními stroji a jednotkami nahrazeno jedinou platformou: systémem zenon. Tento komplexní software pro vysoký stupeň automatizovaného provozu strojů a systémů pokrývá všechny tradiční úrovně řídicího systému procesů, tedy SCADA, HMI i PLC.
Tento způsob implementace významně snižuje počet rozhraní mezi různými systémy. Zjednodušuje konfiguraci a údržbu celého systému a snižuje počet možných zdrojů chyb.
Tradice přenesená do budoucnosti
Techničtí pracovníci ze společnosti ematric použili celou řadu funkčností nabízených systémem zenon. Vedle rozhraní do systému SAP nasadili také modul modelování zařízení a rozšířený trend, abychom uvedli alespoň některé z nich. Protože je v celém systému nasazeno kolem 40 řídicích jednotek (PLC) různých výrobců, inženýři z ematricu použili pro optimální integraci veškerého hardwaru také vestavěné softwarové moduly jako VSTA a softwarové PLC zenon Logic.
Implementace byla uskutečněna paralelně s výstavbou nového výrobního závodu. Vedle programování řídicích jednotek a personalizace systému zenon bylo zadáno i vybudování jednotlivých řídicích středisek v rámci každého závodu. V řídicích střediscích jsou na několika monitorech přehledně zobrazeny všechny provozní stavy. Vzniklé chyby a poruchy jsou okamžitě detekovány, a tak je možné provést okamžitě kroky potřebné k jejich efektivnímu vyřešení. Díky hlášením zasílaným prostřednictvím modulu zenon Message Control a díky přístupu přes webové služby mohou být chyby vyřešeny velice rychle a lze se tak vyhnout nadbytečným prostojům.
Se standardizovaným uživatelským rozhraním a rozsáhlými možnostmi reportingu, který může zahrnovat i historická data, podporuje systém zenon zaměstnance při optimálním řízení výroby. „Plně integrovaný tok dat napříč všemi systémy nám umožňuje řídit celou továrnu s minimálním úsilím,“ potvrzuje Karl Christian Handl. „Integrací všech systémů do platformy zenon můžeme velmi rychle reagovat na poruchy a provádět optimalizaci procesu.“ Navíc data z testů a vlastní výroby, sebraná do rozličných reportů, pomáhají optimalizovat kvalitu a výrobní náklady.
Po měsíčním zkušebním provozu přešla továrna na plnou výrobu bez nutnosti dalších updatů. Od té doby je Tyrolská slanina CHZO vyráběna v nové továrně firmy HANDL TYROL v rakouském městě Haiming za použití neporazitelné kombinace tradičních metod a nejmodernějších technologií. Kompletní automatizace se systémem zenon zajistila vysokou efektivitu operací, umožnila další růst a zajistila konzistentní vysokou kvalitu produktu. Jak uvedl Karl Christian Handl při slavnostním otevření nového provozu: „Vize se přeměnila ve skutečnost – tradice se stává budoucností. Plně integrovaný tok dat napříč všemi systémy nám umožňuje řídit celou továrnu s minimálním úsilím.“
Autor: Peter Kemptner, Rakousko